CNC machining titanium refers to the process of using computer numerical control (CNC) machines to shape and finish titanium parts. Titanium is a highly desirable material in various industries due to its unique properties.
Advantages of CNC machining titanium
- Strength and durability: Titanium is known for its exceptional strength-to-weight ratio, making it ideal for applications where high strength and reliability are required.
- Corrosion resistance: It has excellent resistance to corrosion, even in harsh environments, making it suitable for use in aerospace, medical, and marine industries.
- Biocompatibility: In the medical field, titanium is biocompatible, meaning it is well-tolerated by the human body and can be used for implants and surgical instruments.
- High precision: CNC machining allows for extremely accurate and repeatable production of titanium parts, ensuring tight tolerances and consistent quality.
Process of CNC machining titanium
- Design and programming: The first step is to create a detailed design of the titanium part using computer-aided design (CAD) software. The design is then converted into machine-readable code using computer-aided manufacturing (CAM) software.
- Material selection: High-quality titanium stock is selected based on the specific requirements of the part. Titanium comes in different grades and forms, such as bars, plates, and tubes.
- Setup and fixturing: The titanium workpiece is securely clamped or held in place on the CNC machine using appropriate fixtures. This ensures stability during machining and accurate positioning.
- Machining operations: The CNC machine performs various cutting operations, such as milling, turning, drilling, and grinding, to shape the titanium part according to the programmed instructions. High-speed cutting tools and coolants are often used to optimize the machining process.
- Inspection and quality control: After machining, the titanium part is inspected for dimensional accuracy, surface finish, and other quality parameters. Advanced inspection tools such as coordinate measuring machines (CMMs) may be used to ensure compliance with specifications.
- Finishing and post-processing: Depending on the application, the titanium part may undergo additional finishing processes such as polishing, anodizing, or heat treatment to enhance its appearance and performance.
Applications of CNC machined titanium parts
- Aerospace industry: Titanium is widely used in aircraft and spacecraft components due to its lightweight and high strength. CNC machined titanium parts can be found in engine parts, airframe structures, and landing gear.
- Medical field: Titanium implants, such as hip and knee replacements, dental implants, and surgical instruments, are often manufactured using CNC machining. The biocompatibility and durability of titanium make it an ideal material for medical applications.
- Automotive industry: Titanium is used in high-performance racing cars and luxury vehicles for its strength and lightweight properties. CNC machined titanium parts can be found in engine components, exhaust systems, and suspension parts.
- Marine industry: Titanium is resistant to saltwater corrosion and is used in marine applications such as boat propellers, hull fittings, and offshore oil and gas equipment.
- Industrial machinery: Titanium parts are used in various industrial machinery and equipment, such as pumps, valves, and chemical processing equipment, where strength, corrosion resistance, and high temperature resistance are required.
CNC machining titanium offers many advantages, including high strength, corrosion resistance, biocompatibility, and precision. It is a valuable manufacturing process for producing complex titanium parts for a wide range of industries.

Company profile
Qixin titanium Co.Ltd, is a leading manufacturer specializing in coated titanium anode. With an extensive historyand a wealth of expertise, we have been dedicated to providing high-quality products and solutions to variousindustries for many years.Our company was established 2006, and since then, we have accumulated 18 years of valuable manufacturingexperience. This experience has enabled us to master the art and science of producing top-notch coated titaniumanodes that meet the most stringent quality standards.We take pride in our state-of-the -art manufacturing facilities and a team of highly skilled professionals. Ourengineers and technicians are experts in the field, constantly researching and innovating to improve our productsand processes.
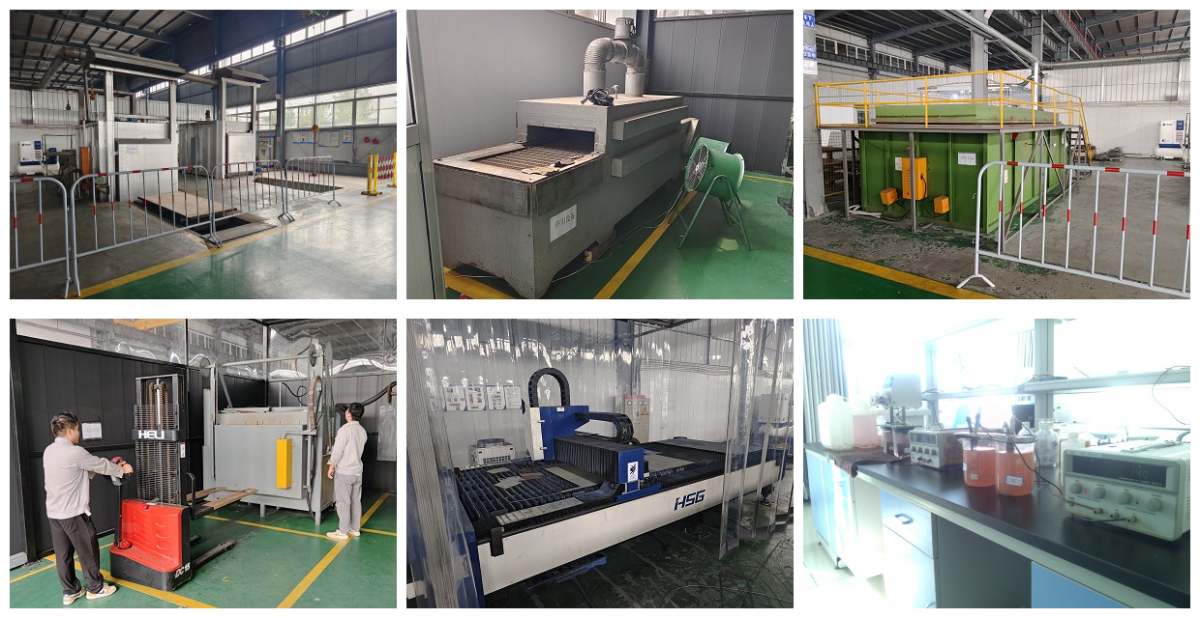
Packing and shipping
(The picture is for your reference) Customized Package Is Available.
Step1: Wrapped by water proof paper
Step2: Bubble papaer
Step3: Plywood case outside to avoid any damage during the shipment.
Or packed as customer’s requirement.
Shipping :by air,by sea,Ems,Fedex or Dhl.
Delivery:15 working days after payment.
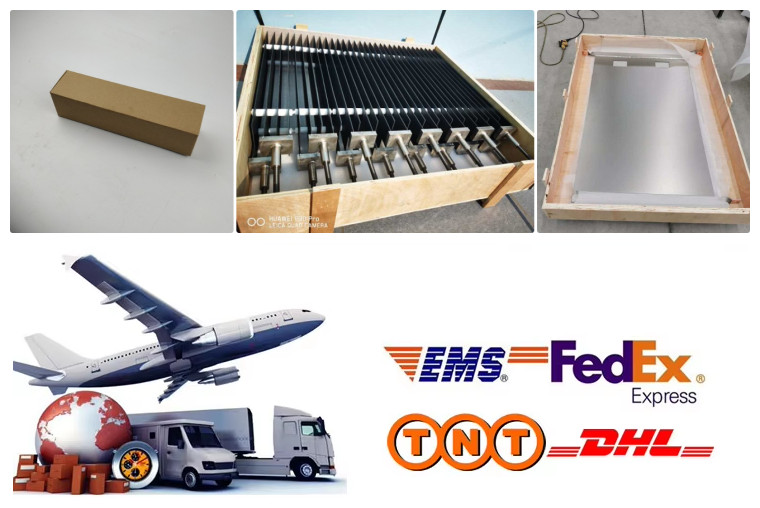
FAQ
1. How to ensure the product quality?
All products make 100% inspection before shipment also we can provide the MTC Material Test Certification.
2. Can you print our Logo on the products?
Sure, and we welcome the customerized products.
3.What about the payment terms?.
T/T, L/C, Paypal, Western Union, Escrew and MoneyGram etc are all accepted.
4.What is the necessary information for an inquiry?
Product name, specification, material grade and quantity.
5.Can we get a free sample before cargo production?
Sure.