Titanium wire and titanium alloy wire materials represent a distinguished category within the titanium material spectrum, cherished for their distinctive attributes that endow them with versatility across a multitude of sectors. These wire materials predominantly fall into two principal classifications: pure titanium and titanium alloys. The latter, characterized by varying compositions and room temperature microstructures, encompasses a diverse array of types. The final forms of these wire materials typically manifest in two distinct conditions: a hard state, denoted as ‘Y’, and an annealed state, labeled as ‘M’.
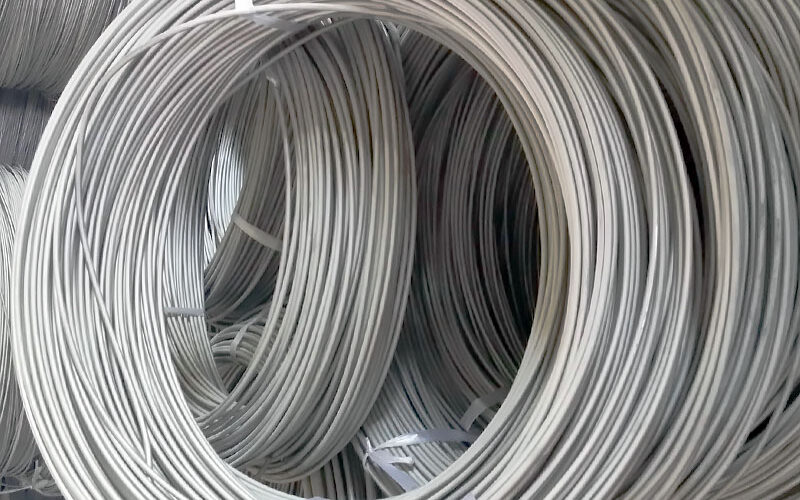
Production process of titanium wire.
- Raw material preparation: Select high-purity titanium or titanium alloy as the raw material. High-purity materials ensure the quality and performance of the final titanium wire.
- Melting: The raw materials are melted to produce titanium ingots or titanium alloy ingots. This step often uses advanced melting methods such as vacuum arc melting or electron beam melting to ensure the homogeneity and purity of the molten metal.
- Forging: The titanium ingots or titanium alloy ingots are forged to improve their microstructure and properties. Forging can refine the grain structure, increase the density, and enhance the mechanical strength of the material.
- Hot rolling: The forged billets are hot rolled to produce bars or wires of a certain size. Hot rolling at high temperatures can shape the material and further improve its mechanical properties.
- Drawing: The bars or wires are drawn through a wire drawing machine to obtain titanium wire of the desired diameter. The drawing process gradually reduces the diameter of the material while maintaining its integrity and strength.
- Heat treatment: The titanium wire is subjected to heat treatment to eliminate internal stress and improve its performance. Different heat treatment processes can be used to adjust the hardness, ductility, and other properties of the wire.
- Surface treatment: According to needs, the titanium wire is subjected to surface treatment such as pickling or brightening to improve its surface quality and corrosion resistance. Surface treatment can remove impurities and oxides on the surface of the wire and give it a smooth and shiny appearance.
Titanium wire can be classified into the following categories
- By material
Pure titanium wire: Composed mainly of pure titanium, it exhibits the basic properties of titanium such as low density, high strength, and good corrosion resistance. Different grades like TA0, TA1, TA2, and TA3 are available based on purity levels.
Titanium alloy wire: Formed by adding other alloying elements such as aluminum, vanadium, molybdenum, and chromium to titanium. Common titanium alloy wires include Ti-6Al-4V (TC4), Ti-5Al-2.5Sn, Ti-15Mo, etc. Each alloy has unique properties depending on the alloy elements and their proportions. - By form
Titanium coiled wire: Usually wound into a coil for easy storage, transportation, and use. The diameter and length of the coil can be customized according to requirements.
Straight titanium wire: Presented in a straight line shape. It is often used in applications that require linear materials, such as making welding wires or springs. - By surface treatment
Pickled titanium wire: Undergoes pickling treatment to remove surface impurities and oxides, resulting in a matte finish.
Bright titanium wire: Treated to have a shiny surface, enhancing its aesthetic appeal and corrosion resistance. - By usage
Structural titanium wire: Used for manufacturing structural components and fasteners.
Welding titanium wire: Serves as a filler material for welding electrodes.
Titanium wire has numerous outstanding performance advantages. Firstly, the density of titanium wire is relatively low, about 4.51g/cm³, which is approximately 43% lighter than steel. However, its mechanical strength is similar to that of steel and is twice that of aluminum and five times that of magnesium. Secondly, titanium wire has high temperature resistance, with a melting point as high as 1942K, nearly 1000K higher than gold and nearly 500K higher than steel. Thirdly, titanium wire has good corrosion resistance and can be used stably for a long time in corrosive environments such as acids and alkalis. In addition, titanium wire also has good biocompatibility, is non-magnetic, has a low elastic modulus, and has strong damping resistance. These properties make titanium wire widely used in many fields.
Company profile
Qixin titanium Co.Ltd, is a leading manufacturer specializing in coated titanium anode. With an extensive historyand a wealth of expertise, we have been dedicated to providing high-quality products and solutions to variousindustries for many years.Our company was established 2006, and since then, we have accumulated 18 years of valuable manufacturingexperience. This experience has enabled us to master the art and science of producing top-notch coated titaniumanodes that meet the most stringent quality standards.We take pride in our state-of-the -art manufacturing facilities and a team of highly skilled professionals. Ourengineers and technicians are experts in the field, constantly researching and innovating to improve our productsand processes.
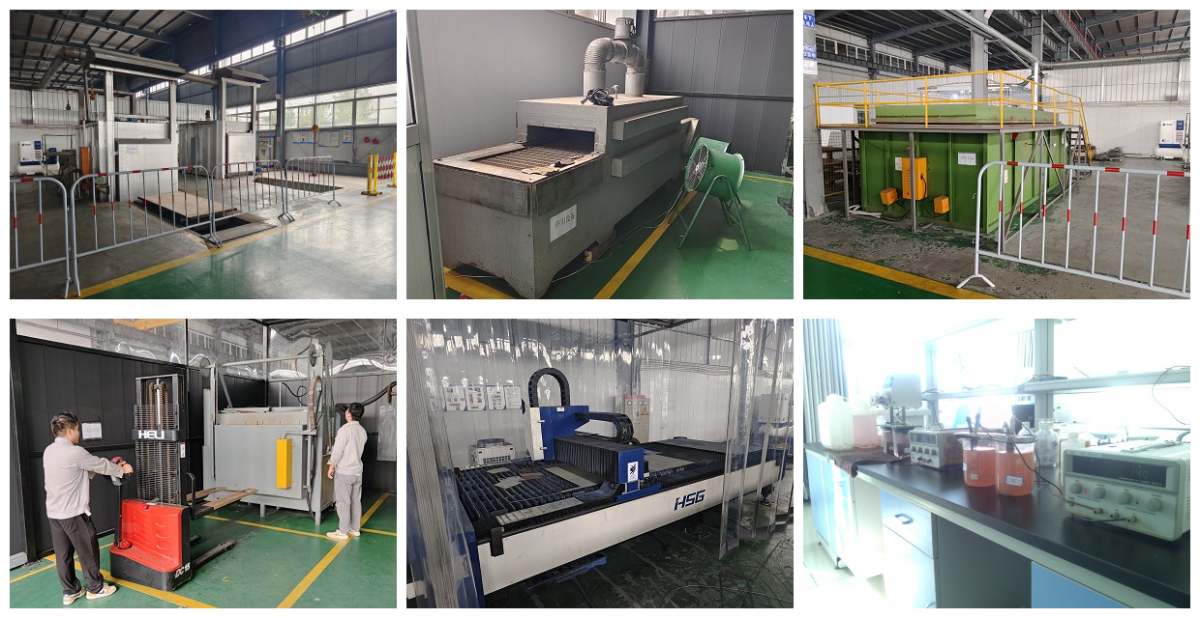
Packing and shipping
(The picture is for your reference) Customized Package Is Available.
Step1: Wrapped by water proof paper
Step2: Bubble papaer
Step3: Plywood case outside to avoid any damage during the shipment.
Or packed as customer’s requirement.
Shipping :by air,by sea,Ems,Fedex or Dhl.
Delivery:15 working days after payment.
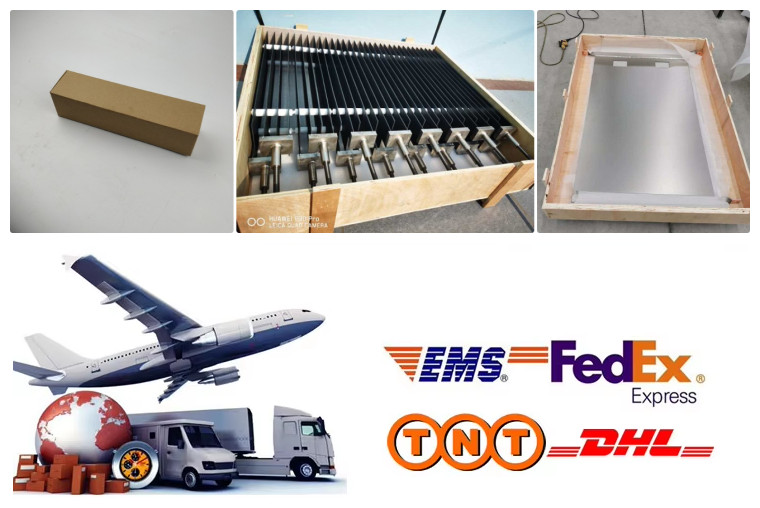
FAQ
1. How to ensure the product quality?
All products make 100% inspection before shipment also we can provide the MTC Material Test Certification.
2. Can you print our Logo on the products?
Sure, and we welcome the customerized products.
3.What about the payment terms?.
T/T, L/C, Paypal, Western Union, Escrew and MoneyGram etc are all accepted.
4.What is the necessary information for an inquiry?
Product name, specification, material grade and quantity.
5.Can we get a free sample before cargo production?
Sure.
Contact Us
For more information or to request a quote, please reach out to us:
Email: info@mmo-anode.com
Phone: +86 9173307518, +86 18395477537, +86 13759759535, +86 18991769543, +86 15891475263
WhatsApp: +86 18395477537, +86 13759759535, +86 18991769543, +86 15891475263