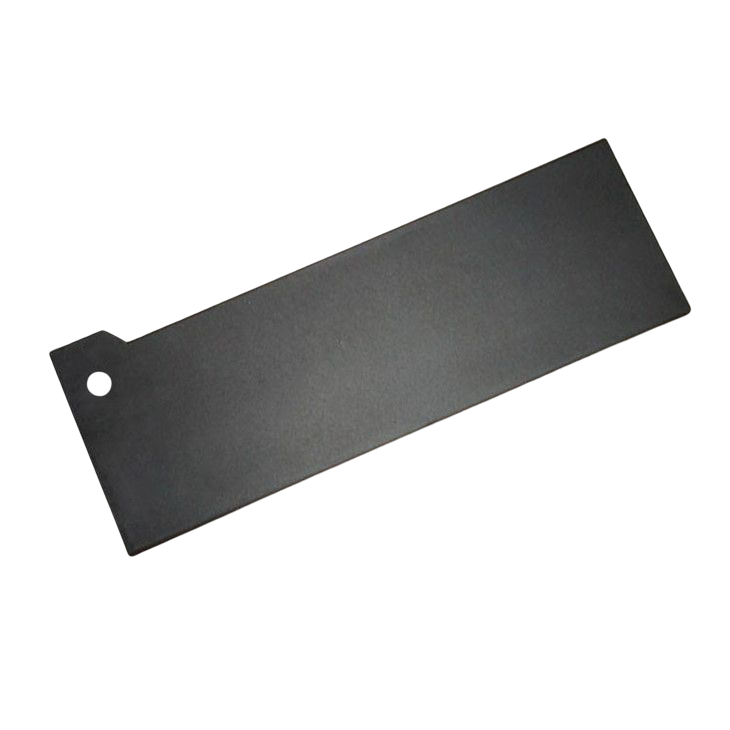
Iridium coated titanium anodes are widely used in various electrochemical processes due to their exceptional durability and performance. The question of whether these anodes can be reused is of significant interest to industries seeking to optimize their operations and reduce costs. Iridium coated titanium anodes can indeed be reused, but with some important considerations. The reusability of these anodes depends on factors such as the extent of wear, the specific application, and the quality of the original coating. Proper maintenance and periodic recoating can significantly extend the lifespan of these anodes, making them a cost-effective choice for long-term industrial use. However, it’s crucial to assess the condition of the anodes regularly to ensure they continue to meet performance standards.
Factors Affecting the Reusability of Iridium Coated Titanium Anodes
Coating Integrity and Wear
The reusability of iridium coated titanium anodes largely depends on the integrity of the iridium coating. Over time, the coating may experience wear due to continuous use in electrochemical processes. The rate of wear can vary depending on factors such as current density, electrolyte composition, and operating conditions. When the coating begins to degrade, it can lead to reduced efficiency and potential contamination of the electrolyte. Regular inspection of the anode surface using techniques such as scanning electron microscopy (SEM) or X-ray photoelectron spectroscopy (XPS) can help determine the extent of wear and the remaining thickness of the iridium coating.
Operating Environment
The operating environment plays a crucial role in determining the lifespan and reusability of iridium coated titanium anodes. Harsh conditions, such as high temperatures, extreme pH levels, or the presence of corrosive substances, can accelerate the degradation of the coating. In contrast, anodes used in milder environments may maintain their integrity for longer periods. It’s essential to consider the specific application and adjust maintenance schedules accordingly. For instance, anodes used in chlor-alkali production may require more frequent inspection and potential recoating compared to those used in less aggressive environments.
Quality of Initial Coating
The quality of the initial iridium coating significantly impacts the anode’s reusability. High-quality coatings applied using advanced techniques such as magnetron sputtering or thermal decomposition tend to have better adhesion to the titanium substrate and improved uniformity. These characteristics contribute to enhanced durability and resistance to wear. Anodes with superior initial coatings are more likely to withstand multiple use cycles and may be candidates for successful recoating when necessary. When considering the reuse of iridium coated titanium anodes, it’s crucial to assess the original manufacturing process and coating quality to make informed decisions about their potential longevity.
Maintenance and Recoating Procedures for Iridium Coated Titanium Anodes
Regular Cleaning and Inspection
Proper maintenance is key to extending the lifespan and ensuring the reusability of iridium coated titanium anodes. Regular cleaning is essential to remove any accumulated deposits or contaminants that may affect the anode’s performance. Depending on the application, this may involve chemical cleaning, ultrasonic cleaning, or mechanical methods. After cleaning, thorough inspection should be carried out to assess the condition of the coating. Visual inspection can reveal obvious signs of wear or damage, while more advanced techniques such as electrochemical impedance spectroscopy (EIS) can provide insights into the coating’s integrity and electrochemical properties.
Recoating Process
When the iridium coating on a titanium anode has degraded to a point where its performance is compromised, recoating can be a viable option to extend its usability. The recoating process typically involves removing any remaining iridium coating, preparing the titanium substrate, and applying a new layer of iridium. This process may include steps such as surface etching, electrodeposition, or thermal decomposition of iridium precursors. The choice of recoating method depends on factors such as the desired coating thickness, adhesion requirements, and the specific application of the anode. It’s important to note that the recoating process should be carried out by experienced professionals to ensure the quality and performance of the renewed anode.
Performance Evaluation After Recoating
After recoating an iridium titanium anode, it’s crucial to evaluate its performance to ensure it meets the required standards. This evaluation may include electrochemical testing to assess parameters such as oxygen evolution potential, current efficiency, and stability. Accelerated life testing can also be performed to predict the longevity of the recoated anode under simulated operating conditions. By comparing the performance of recoated anodes with new ones, operators can make informed decisions about the cost-effectiveness of reusing and recoating versus purchasing new anodes. In many cases, properly recoated anodes can perform comparably to new ones, making reuse a viable and economical option.
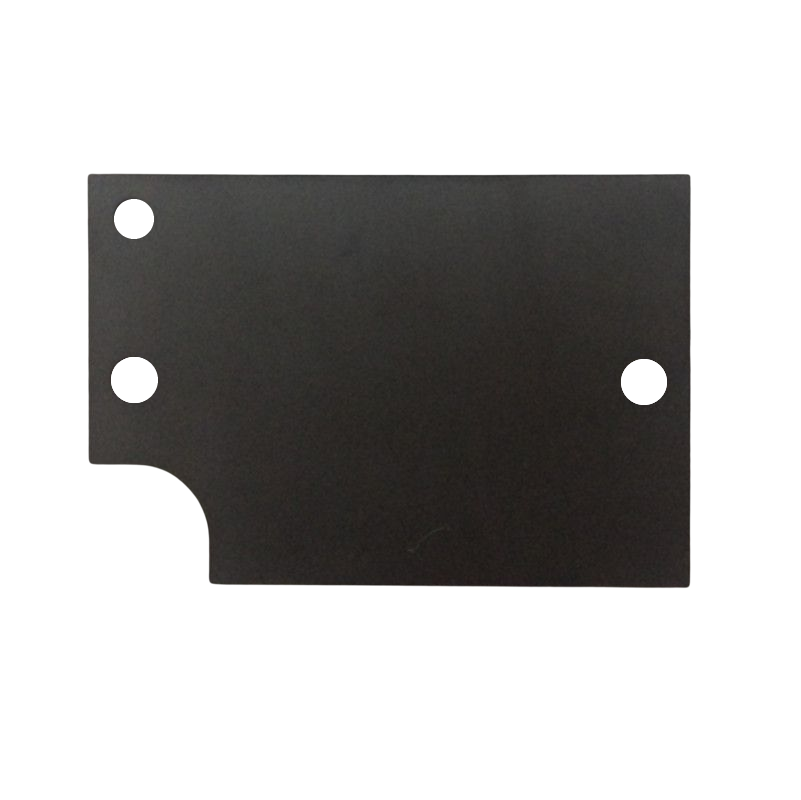
Economic and Environmental Considerations of Reusing Iridium Coated Titanium Anodes
Cost-Benefit Analysis
Reusing iridium coated titanium anodes can offer significant economic benefits to industries relying on electrochemical processes. The initial investment in high-quality anodes is substantial, primarily due to the cost of iridium, a rare and expensive metal. By extending the lifespan of these anodes through proper maintenance and recoating, companies can amortize the initial cost over a longer period. A comprehensive cost-benefit analysis should consider factors such as the frequency of recoating, the cost of downtime during maintenance, and the potential for improved efficiency with newer coating technologies. In many cases, the long-term savings from reusing and recoating anodes can outweigh the cost of frequent replacements, especially in large-scale industrial applications.
Sustainability and Resource Conservation
The reuse of iridium coated titanium anodes aligns with principles of sustainability and resource conservation. Iridium is one of the rarest elements in the Earth’s crust, and its extraction and processing have significant environmental impacts. By extending the life of iridium coatings through reuse and recoating, industries can reduce the demand for new iridium production, thereby minimizing the associated environmental footprint. Additionally, the titanium substrate of these anodes is highly recyclable, further contributing to resource efficiency. Embracing a circular economy approach by reusing and recycling these valuable components can help industries reduce their ecological impact while maintaining high performance standards in their electrochemical processes.
Regulatory Compliance and Industry Standards
When considering the reuse of iridium coated titanium anodes, it’s essential to ensure compliance with relevant regulatory requirements and industry standards. Different sectors, such as water treatment, chlor-alkali production, or metal electrowinning, may have specific guidelines regarding the use and maintenance of electrodes. Some regulations may mandate regular testing and certification of reused or recoated anodes to ensure they meet performance and safety standards. Staying informed about these requirements and working closely with regulatory bodies can help industries implement sustainable anode reuse practices while maintaining compliance. Moreover, adhering to high standards in anode reuse and maintenance can contribute to improved industry reputation and potentially open doors to environmentally conscious markets.
In Summary
iridium coated titanium anodes can indeed be reused, offering significant economic and environmental benefits to various industries. The key to successful reuse lies in proper maintenance, timely recoating, and careful performance evaluation. By considering factors such as coating integrity, operating environment, and initial quality, companies can maximize the lifespan of these valuable components. The reuse of iridium coated titanium anodes not only reduces costs but also aligns with sustainability goals by conserving rare resources. As technology advances and recoating processes improve, the potential for extending anode life and performance continues to grow, making reuse an increasingly attractive option for forward-thinking industries.