Electrophoretic coating is a coating method that uses an applied electric field to make the particles such as pigments and resins suspended in the electrophoretic solution migrate directionally and deposit on the substrate surface of one of the electrodes.
- Principle of electrophoretic coating
During the electrophoretic coating process, charged paint particles move towards the opposite electrode under the action of an electric field and deposit on the electrode surface to form a coating. Specifically, the object to be coated is immersed as a cathode or anode in a water-soluble paint. After connecting to direct current, under the action of an electric field, the particles such as resin and pigment in the paint will move and deposit on the surface of the object to be coated, forming a uniform coating. - Characteristics of electrophoretic coating
High efficiency: Electrophoretic coating has a fast speed and can realize automated continuous production, greatly improving production efficiency.
Uniform coating: Due to the action of an electric field, paint particles can be uniformly deposited on the surface of the object to be coated, forming a coating with uniform thickness and a smooth and flat surface.
Strong adhesion: The adhesion between the electrophoretic coating and the surface of the object to be coated is strong and not easy to fall off.
Good corrosion resistance: The electrophoretic coating has good corrosion resistance and can effectively protect the object to be coated.
Environmental protection: During the electrophoretic coating process, the utilization rate of paint is high, the amount of wastewater discharged is small, and the pollution to the environment is small. - Application fields of electrophoretic coating
Electrophoretic coating is widely used in industries such as automobiles, home appliances, hardware, and machinery. In automobile manufacturing, electrophoretic coating is one of the main coating methods for car body primers and can provide good anti-corrosion protection for the car body. In the home appliance industry, electrophoretic coating can be used for the coating of product casings such as refrigerators, washing machines, and air conditioners, improving the appearance quality and corrosion resistance of products.
Titanium anode for electrophoretic coating
Titanium anode for electrophoretic coating is an efficient component of electrophoretic coating system. It is mainly composed of titanium substrate and precious metal oxide electrochemical active layer covering it. Compared with traditional anodes, this anode has better cost performance. Since the chlorine content has a very obvious corrosion effect on stainless steel anodes, while titanium-based oxide anodes are almost unaffected by it, it is more stable and durable in the electrophoretic coating process.
One of the main advantages of titanium-based oxide anodes in the electrophoretic coating process is their adaptability to current pulses. The size of this anode is stable, and the titanium substrate is always in a non-loss state during production, so it has a long service life. Using this anode can avoid frequent replacements, thereby stabilizing normal production, simplifying management, and directly creating significant economic benefits.
Titanium anodes for cathodic electrophoretic coating have various shapes such as tubular, strip, mesh, and flat plate (thickness 0.65-5mm), and can be processed into any shape according to user needs. These anodes are widely used in fields such as electrophoretic coating, electrodialysis, and organic electrosynthesis.
- Characteristics of titanium anode
Good corrosion resistance: Titanium anode has excellent corrosion resistance in the electrolyte solution of electrophoretic coating, can work stably for a long time, reduces the replacement frequency of electrodes and lowers production costs.
High catalytic activity: The surface of titanium anode is usually coated with precious metal oxide coatings such as ruthenium-iridium oxide, which has high catalytic activity and can promote the electrochemical reaction in the electrophoretic coating process and improve the coating efficiency and quality.
Good dimensional stability: Titanium anode is not easy to deform during use and can maintain a stable size and shape to ensure the uniformity of electrophoretic coating.
Good electrical conductivity: Titanium anode has good electrical conductivity and can effectively transfer current to ensure the smooth progress of electrophoretic coating. - The role of titanium anode in electrophoretic coating
Providing electric field: As the anode in electrophoretic coating, titanium anode and cathode (coated object) together form an electric field, so that paint particles move and deposit on the surface of the coated object under the action of electric field.
Promoting electrochemical reaction: The precious metal oxide coating on the surface of titanium anode can catalyze the electrochemical reaction in the electrophoretic coating process, such as the reaction of oxygen precipitation, etc., and improve the coating efficiency and quality.
Controlling coating thickness: By adjusting the distance between titanium anode and coated object and the electric field strength, the thickness of electrophoretic coating can be controlled to meet the coating requirements of different products. - Maintenance and care of titanium anode
Regular cleaning: During use, some impurities and sediments will accumulate on the surface of titanium anode, affecting its performance. Therefore, titanium anode needs to be cleaned regularly to remove impurities and sediments on the surface.
Avoid collision: Titanium anode should avoid collision and scratch during installation and use to avoid damage to the coating on the electrode surface.
Control current density: In the electrophoretic coating process, the current density should be controlled within a reasonable range to avoid excessive current density leading to overheating and damage of titanium anode.
Regular inspection: Regularly check the performance and status of titanium anode. If any problem is found, it should be dealt with or replaced in time.
Who we are?
Qixin titanium Co.Ltd, is a leading manufacturer specializing in coated titanium anode. With an extensive historyand a wealth of expertise, we have been dedicated to providing high-quality products and solutions to variousindustries for many years.Our company was established 2006, and since then, we have accumulated 18 years of valuable manufacturingexperience. This experience has enabled us to master the art and science of producing top-notch coated titaniumanodes that meet the most stringent quality standards.We take pride in our state-of-the -art manufacturing facilities and a team of highly skilled professionals. Ourengineers and technicians are experts in the field, constantly researching and innovating to improve our productsand processes.
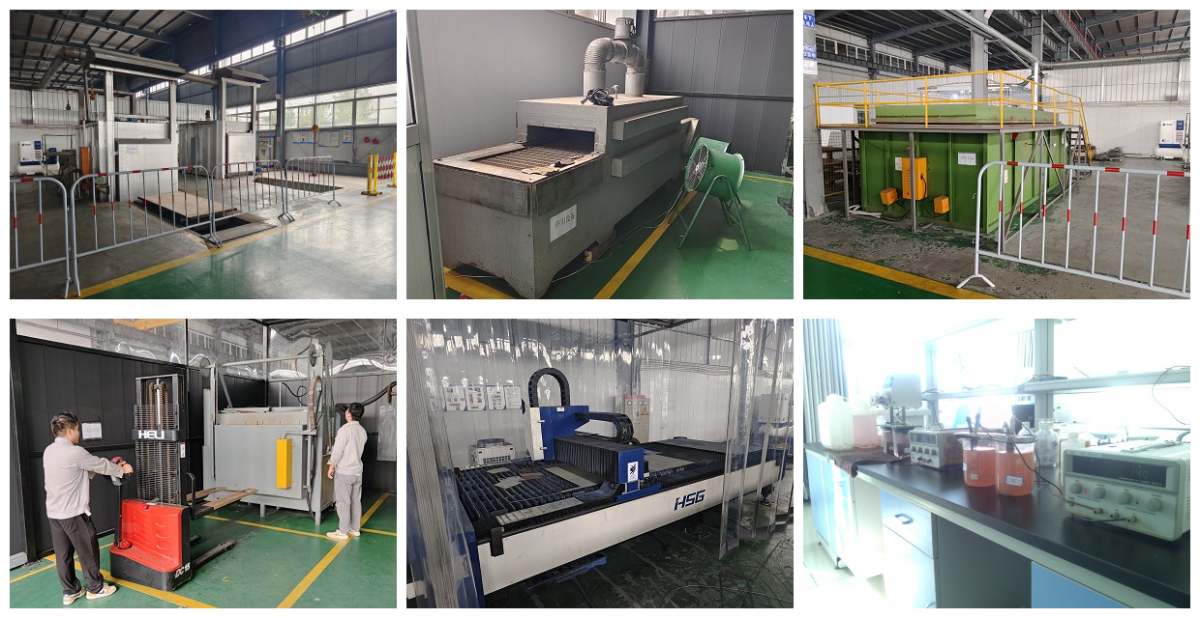
Production
Brush coating.
Specific operation as follows:
Firstly,making the coating solution according to the type and the area of the platinum electrode; secondly ,put the solution on the surface evenly, then put them into the drying furance for drying; thirdly,we need to oxidate in the high temperature oxidation furance;Lastly, dry it to room temperature. Then,repeat these steps until you run out the configuration solution.
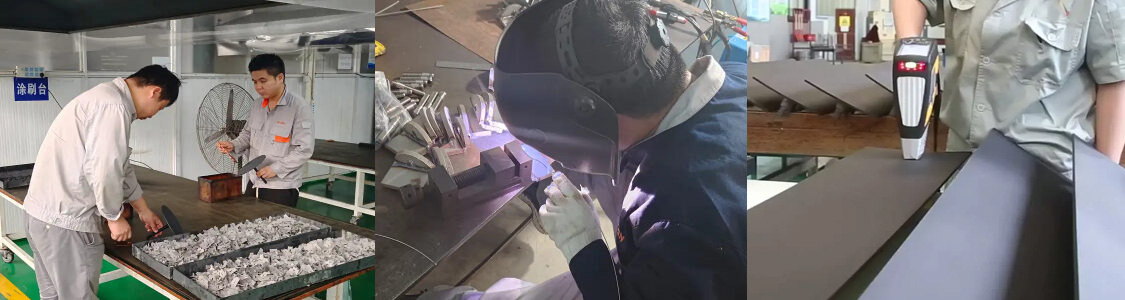
Package and shipping
(The picture is for your reference) Customized Package Is Available.
Step1: Wrapped by water proof paper
Step2: Bubble papaer
Step3: Plywood case outside to avoid any damage during the shipment.
Or packed as customer’s requirement.
Shipping :by air,by sea,Ems,Fedex or Dhl.
Delivery:15 working days after payment.
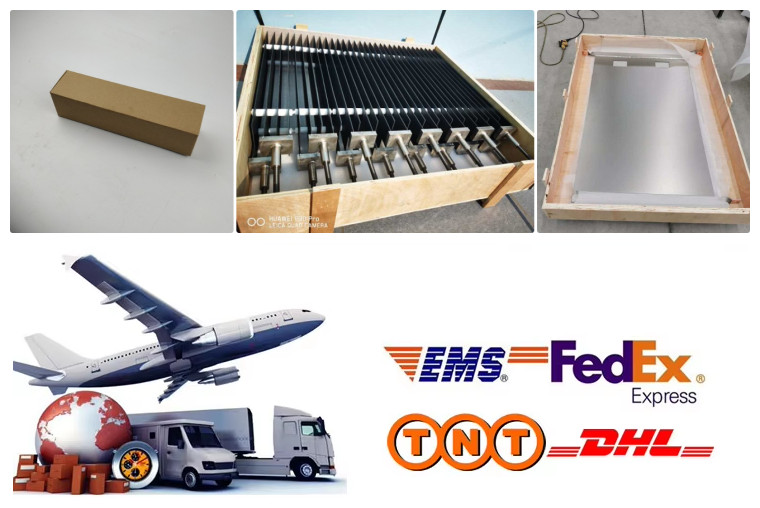
FAQ
1. How to ensure the product quality?
All products make 100% inspection before shipment also we can provide the MTC Material Test Certification.
2. Can you print our Logo on the products?
Sure, and we welcome the customerized products.
3.What about the payment terms?.
T/T, L/C, Paypal, Western Union, Escrew and MoneyGram etc are all accepted.
4.What is the necessary information for an inquiry?
Product name, specification, material grade and quantity.
5.Can we get a free sample before cargo production?
Sure.